Aluminium and Metal Die casting
Our Aluminium and Die Casting Services provide high-quality, custom metal components through precision casting techniques and a trusted global network.
Source Now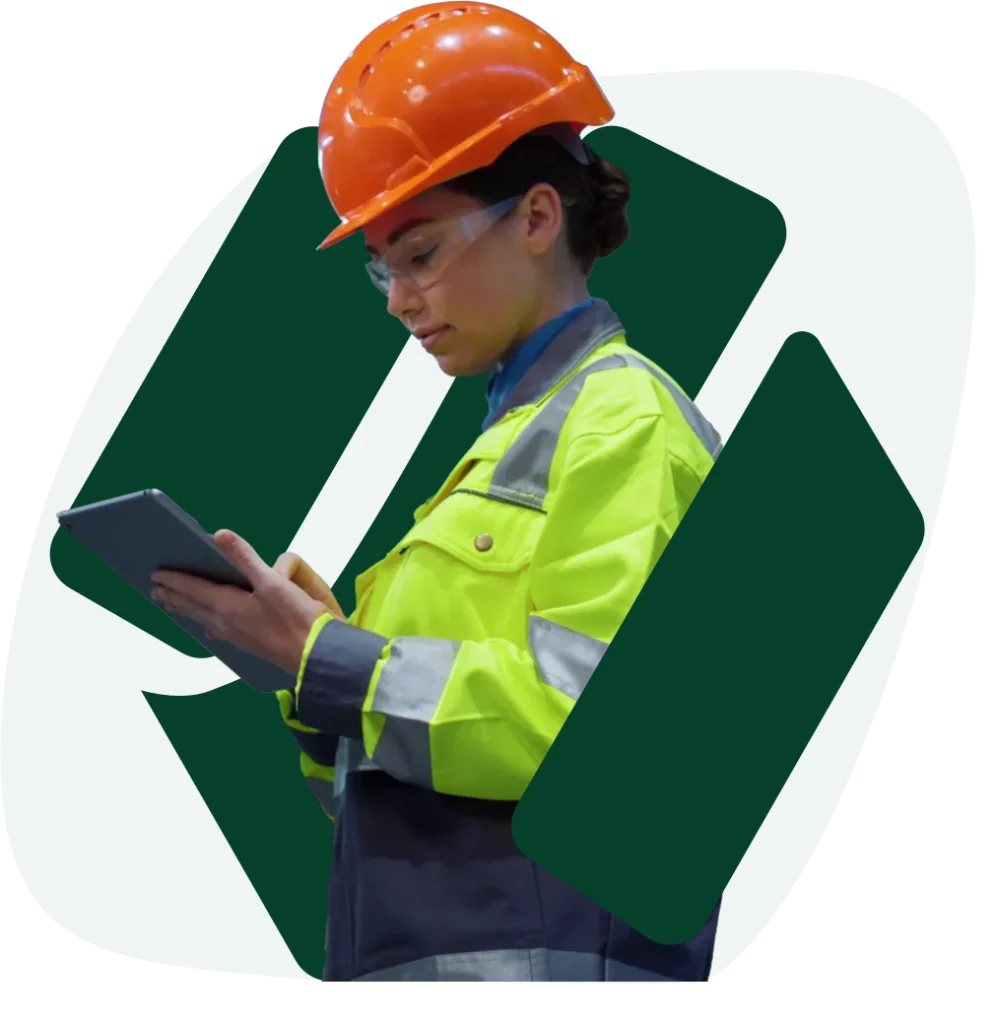
The 4 Main Steps of Die Casting
Aluminium and die casting is a precise and efficient process used to manufacture durable metal components at scale.
-
1
Design & Tooling
CAD models are developed, and a high-precision die mold is created to shape the metal components.
-
2
Material Preparation
Aluminium or other metals are selected, melted at high temperatures, and prepared for casting
-
3
Die Casting Process
Molten metal is injected under high pressure into the die mold, ensuring accuracy and consistency
-
4
Cooling & Finishing
The cast component is cooled, ejected, and undergoes finishing treatments such as machining, polishing, or coating
Most Popular Processes
At SourceFlow, we connect you with trusted, top-tier machine shops, providing CNC machining services that span from basic drill presses to sophisticated 5-axis and 6-axis machining centers.
Material used in die casting projects
The network works well for components that require a specialized color or material options
Aluminium
Properties: Lightweight, corrosion-resistant, excellent thermal and electrical conductivity.
Applications: Automotive, aerospace, and electronic components.
Benefits: Good strength-to-weight ratio, easily machinable, and cost-effective.
Zinc
Properties: High corrosion resistance, good casting fluidity, and ease of machining.
Applications: Small components, electrical fittings, and hardware.
Benefits: Excellent surface finish, high detail resolution, and fast cycle times.
Brass
Properties: High strength, excellent corrosion resistance, and good conductivity.
Applications: Marine, electrical, and decorative parts.
Benefits: Strong, durable, and resistant to harsh environments.
Lead Alloys
Properties: High density, easy to cast, and great for vibration damping.
Applications: Battery parts, radiation shielding, and weights.
Benefits: High performance in specific applications but typically avoided in consumer-facing products due to toxicity concerns.
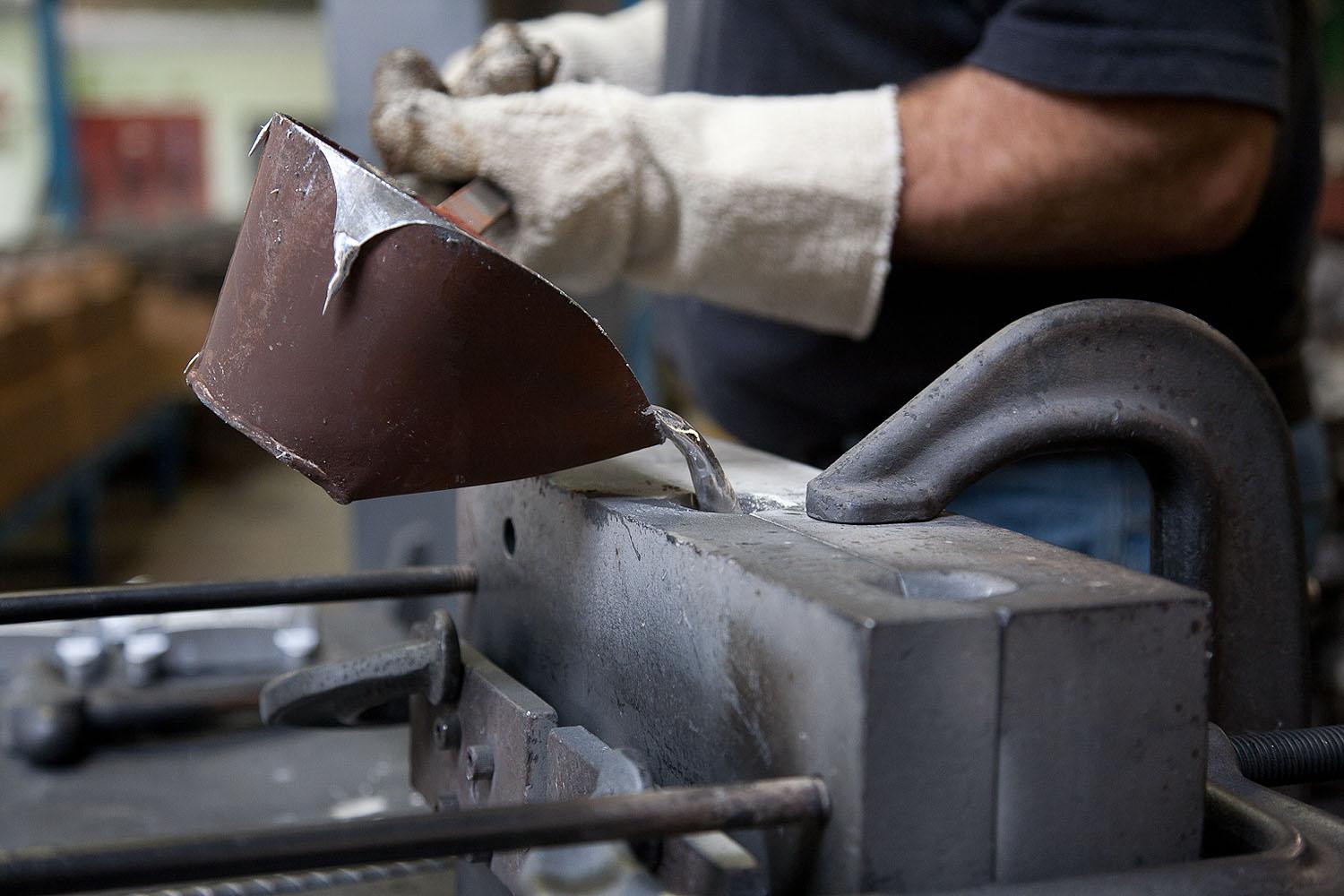
The benefits of Aluminium Casting
One of the biggest advantages is the ability to create complex shapes and intricate designs, which would be difficult or impossible to achieve with other manufacturing processes. Aluminium casting is also highly efficient, allowing for the production of high volumes of parts in a short amount of time. Additionally, aluminium casting can be cost-effective for producing large quantities of parts, as the per-unit cost decreases as the quantity increases.
How can alumiunium casting help you save costs
Plastic injection molding is widely used to produce high-precision parts across various industries.
The process is ideal for creating complex, durable components with tight tolerances. By injecting molten plastic into custom molds, it can produce parts in large volumes, ensuring consistency and cost efficiency.
Plastic injection is commonly used in applications such as automotive parts, medical devices, consumer electronics, packaging, and household products, making it a versatile solution for both functional and aesthetic components.
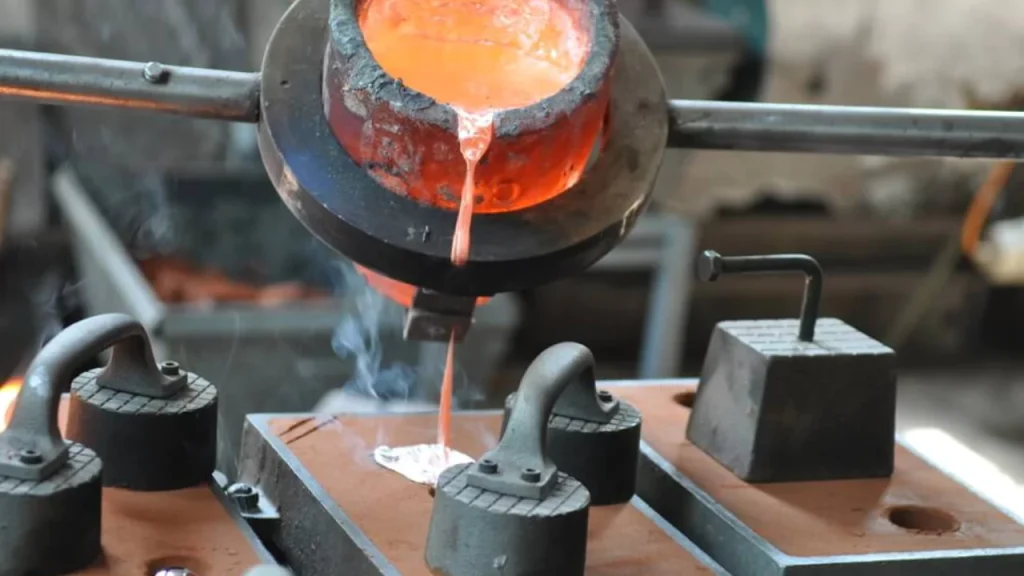
Turnkey Sourcing Solution
Discover how our end-to-end process simplifies supplier selection and procurement
Source now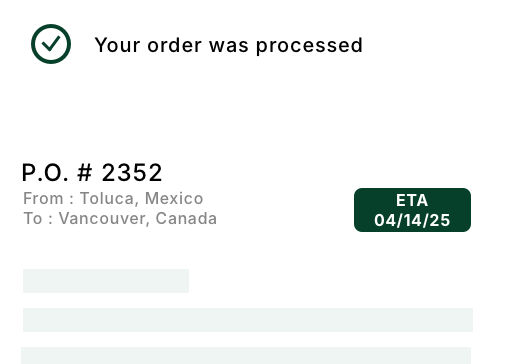
